
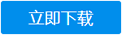
摘要:压铸成型在有色金属成型工艺中占有重要的地位。压铸的工艺特点是压铸所得的工件有较高的强度和硬度,且能够生产形状复杂精度较高的工件,由于生产效率高且适用大批量生产,所以将其作为生产线夹盖板的工艺措施。线夹盖板是高压输电线上用来固定的零件,这里我们使用了铝合金压铸。
分析零件的形状结构和尺寸,开始设计压铸模具。设计内容主要包括:浇注系统的设计、推出机构的设计、模架及成型零件的设计及模体结构的设计。分析压铸件的形状结构与尺寸精度,初步选定合适的压铸机,通过锁模力、压室容量和动模行程的校核确定压铸机的选择是否合理。通过UG绘制出模型的3维视图,并将各个部分分割转入CAD制图当中进行尺寸的标注。
通过查阅资料,模具采用了侧面浇注系统,避免了采用中心浇注时对型芯的直接冲击,增长了模具使用寿命。分析压铸件,得到铸造工艺参数:铸件加工余量取0到0.5mm,收缩率为0.6﹪。模具模体的整体尺寸为400×360mm,可以正常安装到压铸机中。推出机构采用推杆推出机构,使用了6根端面直径为6mm与13根端面直径为8mm的圆截面推杆,复位杆选择了4根端面直径为20mm的圆截面复位杆。对所受承载力进行计算,所用推杆可以达到要求。通过电脑软件进行模拟,模具可以正常运行。
关键词 压铸;压铸模具;铝合金;线夹盖板
目录
摘要
Abstract
1 绪论-1
1.1课题意义-1
1.1.1产品介绍-1
1.1.2 压铸模设计及意义-1
1.2压力铸造的特点及应用-2
1.2.1压铸的特点-2
1.2.2压铸的应用范围-3
1.3 压力铸造的历史及发展趋势-4
1.3.1 压力铸造的历史-4
1.3.2 中国压铸业的现状-4
1.3.3 压力铸造的发展趋势-5
2 压铸模的设计-6
2.1 压铸件的分析-6
2.1.1 压铸件结构、工艺的分析-6
2.1.2 压铸件材料的选择-7
2.2 压铸机的选定-8
2.2.1压铸机锁模力的校核-8
2.2.2 压室容量的校核-9
2.2.3 动模座板行程核算-9
2.3 模具分型面的确定-10
2.4 浇注系统的确定-11
2.4.1 浇口位置的确定-12
2.4.2 内浇口的设计-12
2.4.3 横浇道的设计-14
2.4.4 直浇道的设计-15
2.5 排溢系统的设计-15
2.5.1 集渣包的设计-15
2.5.2 排气槽的设计-17
3推出机构的设计-18
3.1 推出机构的主要组成与分类-18
3.1.1 推出机构的分类-18
3.1.2 推出机构的组成-18
3.2 推出机构的设计要点-18
3.2.1 推出距离的计算-18
3.2.2 推出力的计算-19
3.3 推杆推出机构-19
3.3.1推杆推出的的设置要点-19
3.3.2 推杆的设计-22
3.4 推出机构的复位-23
3.4.1复位杆的设计-23
3.4.2 限位形式-26
4 模架与成型零件的设计-28
4.1 模架的设计-28
4.1.1 模架的构件作用与设计的要点-28
4.1.2 导套及导柱的设计-28
4.2 成型零件的设计-30
4.2.1 成型零件尺寸的计算-31
4.2.2 成型零件装配图-32
4.3 模体的设计-34
4.3.1 模体的尺寸-34
4.3.2模体构件的表面粗糙度和材料选择-35
4.4 模流分析-35
4.4.1 充型顺序的分析-35
4.4.2 空气压力的分析-37
结论-39
致谢-40
参考文献-41