
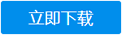
摘要:本课题基于CAD/CAE/CAM对饮水机储水槽进行注塑模具设计。结合零件的使用环境、表面要求、制造成本等因素,选用PP材料。本设计采用一模二腔的模具结构。通过Pro/E进行3D模型和分型面的创建,运用MoldFlow对饮水机储水槽的浇注过程进行模流分析,通过最佳浇口位置、流动性、冷却、翘曲变形等分析来优化模具结构。通过MasterCAM来完成型腔的仿真加工,模拟刀具的行走路径,表明路径选择合理。通过AutoCAD完成注塑模具总装图和零件图的绘制。
MoldFlow分析结果表明:在优化后的注塑工艺参数下,饮水机储水槽的最佳浇口位置位于模型侧壁;流动性分析表明填充时间为0.8099s,气穴较少且大部分分布在分型面处,可以通过排气去除,对塑件的表面质量影响较小;塑件翘曲变形量为0.34mm,冷却分析结果发现冷却回路介质温差为0.5℃,满足要求;冷却分布结果有助于优化冷却管道布局,缩短冷却时间。基于分析的结果利用Pro/E和EMX4.1完成了整套模具设计及校核。加快了产品设计过程,预防了产品缺陷,对实际生产具有一定的指导意义。
关键词 注塑模具;MoldFlow;Pro/E;MasterCAM
目录
摘要
Abstract
1 绪论-1
2 零件模型的建立及工艺性分析-3
2.1 Pro/E软件的简介-3
2.2 模型的建立-3
2.3 工艺性分析-3
2.3.1 塑件的分析-4
2.3.2 PP的性能分析.-4
2.3.3 PP的注塑成型过程及工艺参数-5
3 分型面拟定及注射机的校核-7
3.1 分型面位置的确定-7
3.2 型腔数目及型腔排布形式的确定-8
3.2.1 型腔数目-8
3.2.2 型腔排布形式的确定-8
3.3 注射机型号的确定-9
3.3.1 注塑量的计算-9
3.3.2 浇注系统凝料体积的计算-9
3.3.3 选择注塑机-10
3.3.4 注塑机相关参数的校核-10
4 基于MoldFlow的分析-12
4.1 导入模型并划分网格-12
4.1.1 导入模型-12
4.1.2 网格划分-12
4.2 浇口位置分析-13
4.3 成型窗口分析-13
4.4 充填分析-14
4.4.1 充填时间的分析-14
4.4.2 气穴分布-14
4.5 冷却分析-15
4.5.1 回路冷却介质温度-15
4.5.2 制品最高温度-15
4.6 翘曲分析-16
5 浇注系统的设计-18
5.1 主流道的设计-18
5.2 分流道的设计-18
5.2.1 分流道的布置形式-18
5.2.2 分流道的长度-19
5.2.3 分流道的截面形状-19
5.2.4 分流道的截面尺寸-19
5.2.5 分流道的表面粗糙度和脱模斜度-19
5.3 浇口的设计-19
5.4 冷料穴及拉料杆的设计-20
6 成型零件的结构设计及计算-22
6.1 凹、凸模结构设计-22
6.1.1 凹模结构设计-22
6.1.2 凸模结构设计-22
6.2 成型零件钢材的选用-23
6.3 成型零件尺寸的计算-23
6.3.1 成型零件工作尺寸的计算-23
6.3.2 凹模侧壁厚度及垫板的计算-25
7 模架的确定-27
7.1 各模板尺寸的确定-28
7.1.1 A板尺寸的确定-28
7.1.2 B板尺寸的确定-28
7.1.3 C板尺寸的确定-28
7.2 模架各尺寸的校核-28
7.2.1 模架平面尺寸的校核-28
7.2.2 模架高度尺寸的校核-28
7.2.3 模架开模行程的校核-28
8 脱模推出机构的设计-30
8.1 推出机构的设计原则-30
8.2 脱模力的计算-30
8.3 校核推出机构作用在塑件上的单位压应力-31
8.3.1 推出面积-31
8.3.2 单位压应力的计算-31
9 排气及冷却系统的设计-32
9.1 排气系统的设计-32
9.2 冷却系统的设计-32
9.2.1 冷却系统的设计原则-32
9.2.2 冷却介质的选择-32
9.2.3 冷却系统的简单计算-32
10 仿真加工-35
10.1 MasterCAM的简单介绍-35
10.2 型腔的仿真加工-35
11 模具总装-39
11.1 模具装配过程中的注意事项-39
11.2 模具的装配过程及3D图-39
结论-41
致谢-42
参考文献-43
附录-44