
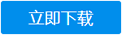
摘 要:服装工业在我国的国民经济中占有很重要的地位,我国服装企业的管理水平普遍不高,尤其体现在生产管理上,生产车间组织不合理、缝制和裁剪工程混乱、作业人员操作随意等情况时常发生。
本文结合DI服饰公司车缝生产线的实际案例说明服装企业生产系统的改进,由分析该公司车缝车间生产现状及存在的问题着手,进而应用工业工程相关知识理论对车缝工程过程进行改善。主要从四个方面进行改进,首先针对车间的整体格局提出了新的车间布置,目的是消除生产组织现场的混乱现象;第二个改善部分是服装车缝部分的时间组织和流水化生产改进,进一步提高生产的流畅性;第三个改善部分是对物料搬运过程进行改善,降低运送的次数和成本,使得整个生产更为流畅;第四部分是使用GDS对生产人员的操作进行持续改善,从而减少浪费、降低工时和生产成本,进而精简人力、提高作业效率。通过以上四部分的改善能有效提高生产效率,降低成本,提高企业的核心竞争力。
关键词:生产系统;车间布置;时间组织;流水生产
ABSTRACT:Garment industry occupies a very important position in China's national economy. China's garment enterprise's management level is generally low, particularly in production management. Unreasonable workshop organizing, disordered sewing and cutting works and casual workers operating happen from time to time.
This paper illustrates the improvement of garment enterprises production systems through the case of DI Company sewing production line. It analyzes the company's sewing workshop production status and problems and improves sewing engineering process based on industrial engineering. This paper improves enterprise production systems mainly from the following four aspects. Firstly, in order to eliminate the chaos in the production organization site, it proposes the new workshop layout of the overall workshop. The second part is to improve the clothing sewing’s time organization and production lines on the purpose of further fluency of production. The third part is the material handling process improvement, reducing the times and cost of transport, making the production more smoothly. The fourth part is to improve operation of the production personnel based on GDS, thereby reducing waste, working hours and production costs, further streamlining manpower, improving operational efficiency. Through the above four parts improvements, the company can effectively improve production efficiency, reduce costs and improve the enterprise's core competitiveness.
Keywords: Production systems; workshop layout; time organization; line production